Expert Inspection Services
Nova Data Testing is a full service nondestructive testing and inspection company ready to provide our customers with the necessary experience to complete any inspection job. We utilize Ultrasonics, Magnetic Particle, Liquid Penetrant, Shearwave, and Visual inspection techniques to test a variety of materials and equipment.
Certified Level III Consulting Services
Nova Data Testing provides Certified Level III NDT Consulting Services to clients that occasionally require a Level III Certification for procedures, training, and testing. We will work directly with you to minimize costs while maintaining compliance with regulations.
INSPECTION PROCEDURES
Ultrasonic thickness testing has been used widely to determine rate of corrosion and erosion, or detecting discontinuities below the surface of a variety of materials. Based on the same principal as sonar, a sound beam is transmitted into a material to determine thickness or soundness, and reflects back to the unit.
Ultrasonic volumetric (shear wave) inspection works on the same basic principles as ultrasonic thickness, however angles are introduces. This allows the sound pulse to travel from a smooth base metal into a weld in a controlled manner. The most commonly occurring defects in welded joints are porosity, slag inclusions, lack of side-wall fusion, and lack of root penetration, undercutting and longitudinal; or transverse cracks.
Liquid Dye Penetrant is mainly used to detect fatigue and stress cracks in ferrous or non-ferrous materials. Penetrant testing will also reveal any cracks, pinholes, laps, seams, leaks as well as grinding cracks. This works on the capillary effect that small voids will draw in the dye. After the dye has been administered, the surface is cleaned. Then a developing agent is applied to expose the residual dye, and the void is revealed.
Because magnetization of certain metals is possible, small particles that are attracted to magnetic fields are applied to the surface of the test object after or during induction of a magnetic field, thereby detecting certain discontinuities which are present in the material. Since magnetic particle testing is capable of revealing discontinuities (variations in material composition) economically, it is one of the most used nondestructive test methods.
Visual testing is the only nondestructive testing technique that can be performed without the aid of other equipment. Because the physical means of visual testing is available to almost everyone and because the process seems so intuitive, some people may assume that the technique itself is not very complex. However it takes a trained eye and experience to conduct a successful visual inspection.
The equipment utilized for Flux Leakage Inspection uses very powerful rare earth magnets in order to near saturate the plate in the area of the scanning head. Coil sensors placed between the poles of the magnetic bridge detect the flux leakage fields and provide a low voltage output signal to the electronic module for processing and real time display. The electronic processing and display module is common to both of the MFE Scanning Systems.
Storage Tank Accelerated Reporting System
A Real Game Changer
SafeView Boiler Inspections
Time Tested Solution
INDUSTRY SECTORS
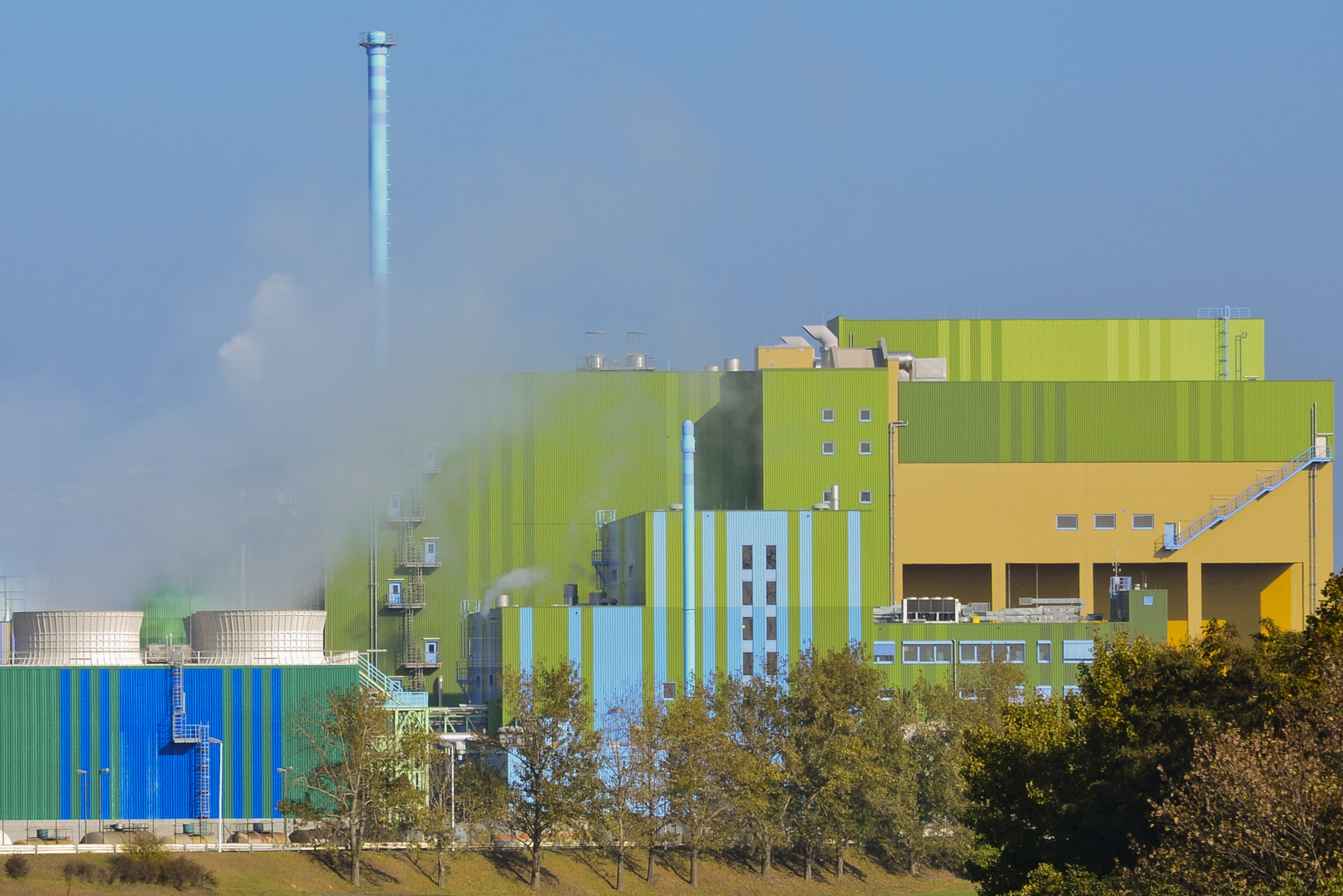
WASTE TO ENERGY
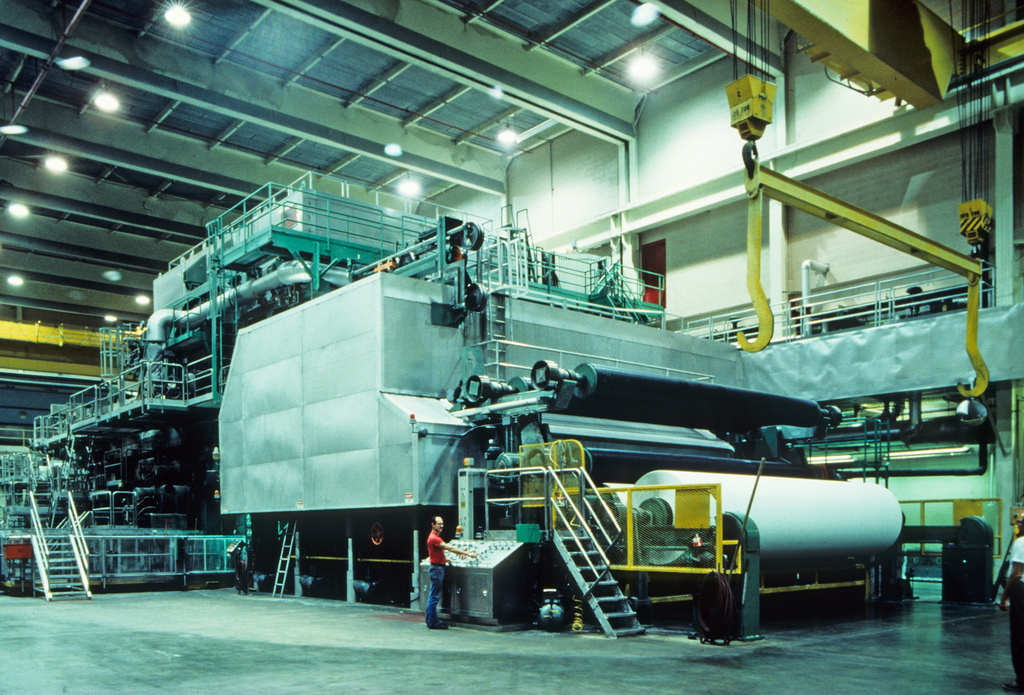
PULP & PAPER
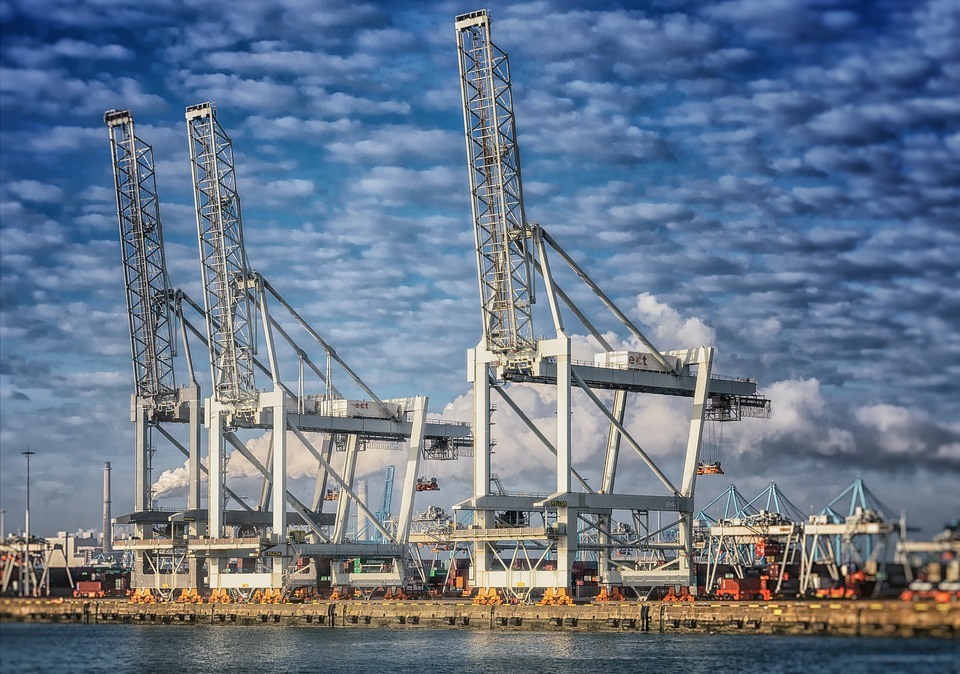
CRANES & RIGGING
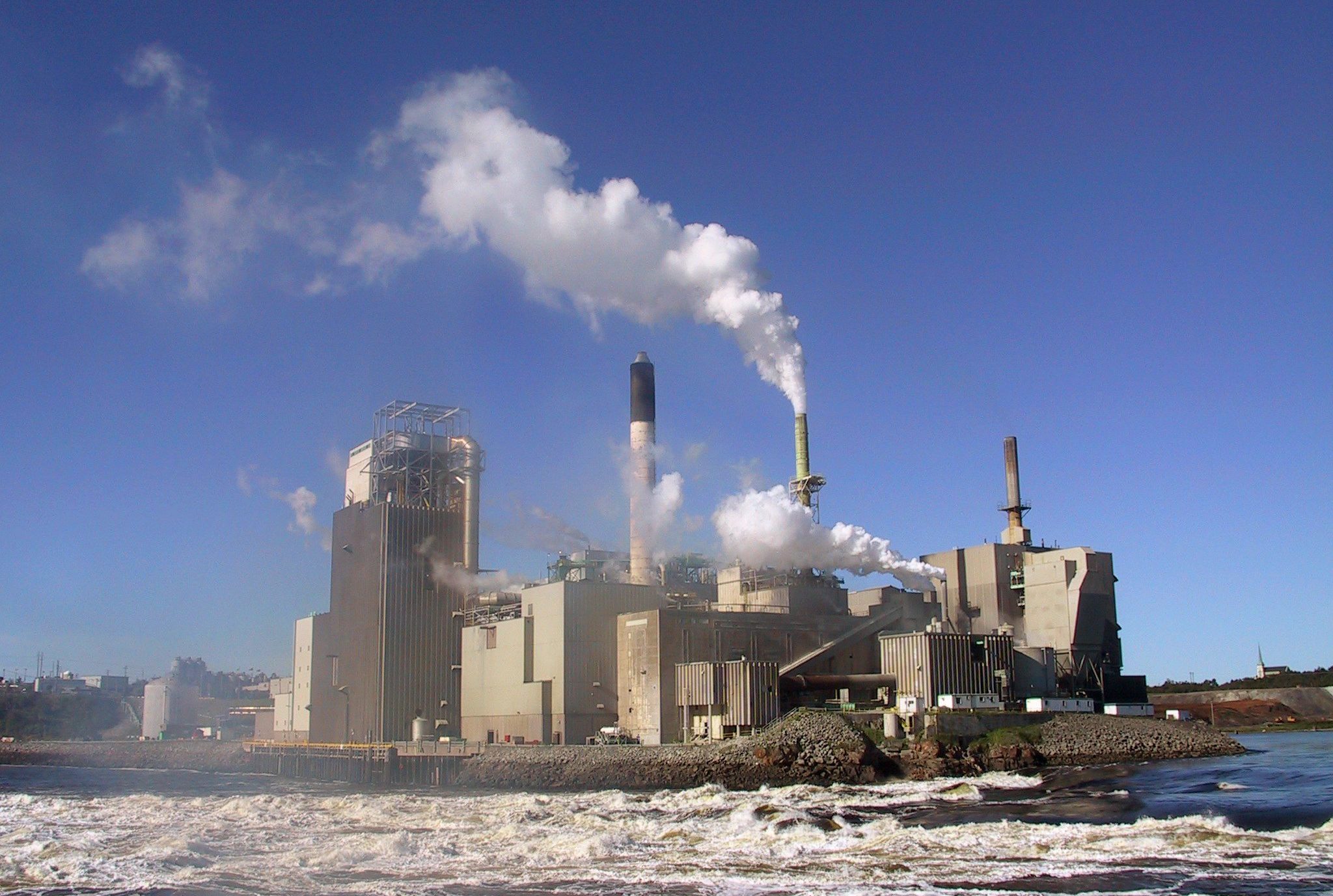
BOILERS & PRESSURE VESSELS
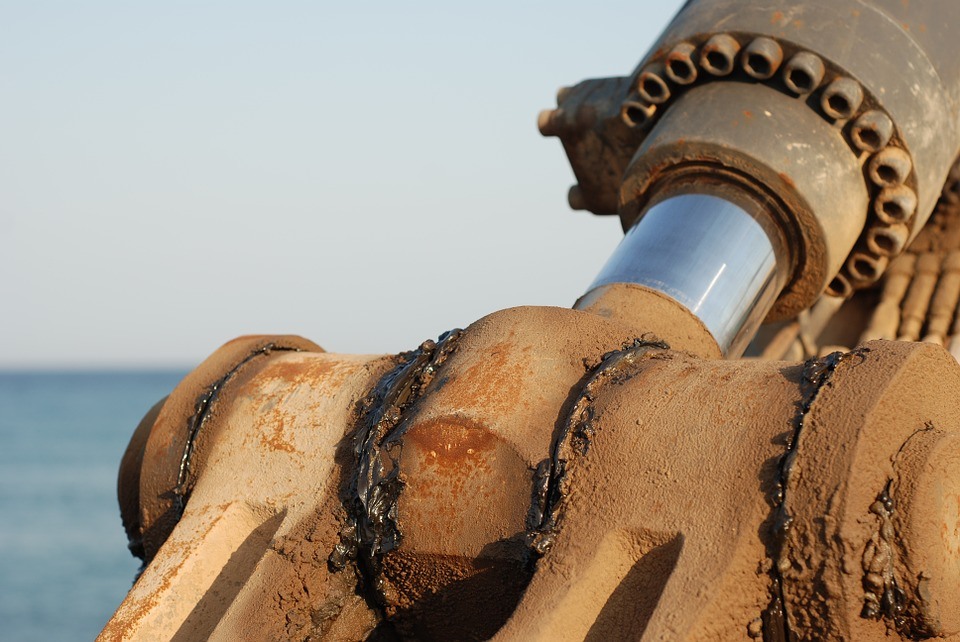
AUXILIARY & SPECIAL EQUIPMENT
INSPECTION PROCEDURES
Ultrasonic Testing
Ultrasonic thickness testing has been used widely to determine rate of corrosion and erosion, or detecting discontinuities below the surface of a variety of materials. Based on the same principal as sonar, a sound beam is transmitted into a material to determine thickness or soundness, and reflects back to the unit. This provides a thickness measurement with the accuracy of +/– .004″ that can be trended for corrosion/erosion rate analysis. The system uses a beam of pulsed ultrasonic energy between 20 kHz to 50MHz in range. The transducer is made of a piezoelectric material which is able to convert mechanical energy into sound waves and then reverse that process, sending the pulse to the ultrasonic equipment. Whatever testing is to be done requires the use of reference standards for calibration and flaw characterization.
In addition to thickness, ultrasonic measurement can also be used to detect delaminated materials or as a “go, no-go” for flaw detection. Delaminated materials are commonly found in pressed plate material. Regular testing of your equipment can detect these anomalies before catastrophic failure of the materials can occur.
Ultrasonic flaw detection of bolts is widely used where safety is a concern due to pressure and stress. It is a cost efficient way to check the integrity of the bolts to minimize downtime and maximize personnel safety.
Nova Data Testing Services utilizes equipment able to “auto calibrate” to the material being inspected and can inspect high temperature equipment. This allows us to inspect a wide variety of materials, while in process, in various environments. Our equipment also allows for thickness measurements through coatings. This means no more damage to the coating in order to acquire an accurate result.
Not only does the equipment record the accurate measurement of the base material, but it will calculate the thickness of the coating.
The application of ultrasonics can be used on metals, nonmetals and composite materials. It is adaptable to substrates, joints and bonds and structural material. Some of the limitations to consider when using ultrasonics is that access to one side of the part is required. There are occasional ambiguous signals that may arise as a result of scatter effects, multiple reflections and geometric complexity. Small or extremely thin parts can be difficult to inspect.
Shearwave Weld Inspection
Ultrasonic volumetric (shear wave) inspection works on the same basic principles as ultrasonic thickness, however angles are introduces. This allows the sound pulse to travel from a smooth base metal into a weld in a controlled manner.
The most commonly occurring defects in welded joints are porosity, slag inclusions, lack of side-wall fusion, and lack of root penetration, undercutting and longitudinal; or transverse cracks.
With the exception of single gas pores all the defects listed are usually well detectable by ultrasonics. Most of the applications are for low-alloy construction quality steels; however welds in aluminum and stainless steels can also be tested. Ultrasonic flaw detection has long been the preferred method for the nondestructive testing of welds. It is a safe, accurate and cost effective method for inspecting these types of weldments.
Ultrasonic weld inspections are performed using a straight beam transducer in conjunction with an angle beam transducer in contact with a plastic wedge. A straight bean transducer is first used to locate any laminations in or near the weld’s heat-affected zone. The angle beam transducer may not return a signal if the sound beam is interrupted by an indication such as an adjacent laminar flaw.
After scanning the heat-affected zone, an angle beam transducer is used to inspect the weld. These transducers use the principles of refraction and mode conversion to produce refracted shear waves into the weld material. The inspection area will include the root, sidewall, crown and heat-affected zones of the weld. The technician will scan the surface of the material around the weld with the transducer. The refracted sound will bounce off a reflector (discontinuity) in the path of the sound beam. By using the proper angle beam, echoes returned from the weld allow the technician to calculate the location and type of discontinuity.
Liquid Dye Penetrant
Liquid Dye Penetrant is mainly used to detect fatigue and stress cracks in ferrous or non-ferrous materials. Penetrant testing will also reveal any cracks, pinholes, laps, seams, leaks as well as grinding cracks. This works on the capillary effect that small voids will draw in the dye. After the dye has been administered, the surface is cleaned. Then a developing agent is applied to expose the residual dye, and the void is revealed.
Fluorescent penetrants contain dyes that are visible only under black light. Black light is a special light with wavelengths between visible and ultraviolet light. Almost invisible, black light causes many materials such as the fluorescent dye to glow in the dark. This fluorescence is normally a brilliant yellow-green that catches the eye and magnifies the indication.
Visible dye penetrants contain dyes that can be seen in visible or white light. They are also known as color contrast or nonfluorescent penetrants. The dye is usually bright red, but different colors can be used for special applications.
Of the two dye penetrants, the visible or color contrast is the simplest to use. No darkened area or black light is needed. However the primary limitation is getting enough contrast or dye into a discontinuity to form an indication. The best sensitivity can be obtained using the fluorescent penetrants.
When using color contrast the surface is covered with penetrating liquid that seeks surface connected cracks. Liquid in cracks bleeds out to stain powder-coating applied to the surface after the removal of excessive liquid film from the surface of the test object.
Penetrant testing can be used in a variety of applications on nonporous and nonabsorbent materials. It can be used on surfaces, entire objects and complex shapes. It can also be used as a control step in metal processing and joining operations. Cracks can be found that are formed during the testing or operation of equipment. Some applications are weldments, joints, tubing, castings and billets. Fuel and liquid-oxygen tanks and vessels, aluminum parts, gas turbine disks and blades and a variety of other components lend themselves well to inspection by the liquid penetrant method.
There are a few limitations such as access being required for surface cleaning and the discontinuity must be surface-connected and open. There may be false indications form shallow scratches and smearing and surface porosity may mask some indications.
Magnetic Particle Testing
Because magnetization of certain metals is possible, small particles that are attracted to magnetic fields are applied to the surface of the test object after or during induction of a magnetic field, thereby detecting certain discontinuities which are present in the material. Since magnetic particle testing is capable of revealing discontinuities (variations in material composition) economically, it is one of the most used nondestructive test methods. However, this test method is limited to disclosing only those methods that are at or near the surface.
Magnetic Particle testing is mainly used to detect fatigue and stress cracks in ferrous materials only. A magnetic field is introduced in the test specimen. Any voids (cracks) will allow the magnetic field to escape the flow of the material, and the applied iron particles will bridge the disturbance.
The objective of magnetic particle testing is to ensure maximum reliability by providing a means of obtaining a visual image of an indication related to a discontinuity in or at the surface of a material. It can also disclose this discontinuity without impairing the material. Magnetic particle testing has the ability to separate acceptable and unacceptable material in accordance with a predetermined set of standards.
Magnetic Particle testing is a simple test method that can be applied to finished products such as billets, hot rolled bars, castings and forgings. Basically it can be used on any ferromagnetic material to find surface and substrate irregularities. It can also be adopted for use on weldments, engine components, shafts and gears.
The medium for Magnetic Particle testing comes in either powder or paste form. In the dry method, the powder is applied in its dry form by dusting or blowing over the specimen. When the wet method is used, the medium is first mixed with a liquid to make a bath, which is then sprayed onto the surface of the test piece.
Since an indication must be readily visible, a good light source is essential. The choice of the particle color is entirely dependent on visibility. The most widely used colors are red, grey and black.
The fluorescent powders and pastes are particles coated with a dye that fluoresces brilliantly under an ultraviolet or black light, thereby increasing visibility.
Some of the limitations involved with magnetic particle inspections are that the specimen must be clean and have a relatively smooth surface. Cracks must be at least 1/64 of an inch in the major dimension. The alignment of the magnetic field and the strength is critical to a proper inspection. Also some metal removal may be required and the demagnetization of the part may be problematic.
Visual Inspection
Visual testing is the only nondestructive testing technique that can be performed without the aid of other equipment. Because the physical means of visual testing is available to almost everyone and because the process seems so intuitive, some people may assume that the technique itself is not very complex.
Visual testing is distinguished from the other methods on nondestructive testing in that it uses the visible light portion of the electromagnetic spectrum. Visible light can only be detected by a sense organ, in other words the eye.
Visual testing was probable the first method of nondestructive testing. It has developed from its ancient origins into many complex and elaborate optical investigation techniques. Some visual tests are based on the simple laws of geometric optics. Others depend on the properties of the light such as its wave nature. A unique advantage of many visual tests is that they can yield quantitative data more readily than other nondestructive tests.
For a variety of objects visual inspections can be used to determine size, shape, quantity, surface finish, fit, function and the presence of surface discontinuities.
In many cases visual testing and inspection is used in conjunction with an applicable code or specification to determine if the structure or part meets certain specific requirements necessary to function as it was intended.
Visible inspection techniques can be enhanced with the use of optical equipment specifically designed to be used as a tool for enhancing the human eye. Such equipment as borescopes (both rigid and flexible), magnifying devices, video and still photos and other machine vision technologies are commonly used to perform these inspections.
Visual criteria are specified for magnetic particle tests and liquid penetrant tests. Light levels, indication sizes, viewing angles, color sensitivity and many other phenomena pertaining to human vision are strictly controlled in order to achieve reliable accuracy in visual tests as well as other nondestructive techniques.
In liquid penetrant tests, visual techniques are used to compare sensitivities of penetrant systems, to detect discontinuities and to verify the cleanliness of the testing materials. In magnetic particle tests, visual acuity of the inspector and the visibility of the test results are as important as they are for liquid penetrant testing.
While the eyes have no match for scanning and evaluating small objects are large structures, trying to recall details such as the exact size, location and orientation after a visual test is difficult. Digital photographs can also be used as a permanent record for visual testing and can be a part of the permanent record of all the inspection data.
Magnetic Flux Leakage
The equipment utilized for the Flux Leakage Inspection of Tank Floors By Nova Data Testing is the MFE 2412/1212 Scanning System or the Silverwing MLF 2000 Tank Floor Scanner.
This equipment uses very powerful rare earth magnets in order to near saturate the plate in the area of the scanning head. Coil sensors placed between the poles of the magnetic bridge detect the flux leakage fields and provide a low voltage output signal to the electronic module for processing and real time display. The electronic processing and display module is common to both of the MFE Scanning Systems.
Proper use of this equipment does not require the setting of calibration thresholds as the amplitude of the signal is an unreliable indicator of remaining wall thickness. Since MFL is a quantitative inspection procedure, no calibration can be made to meet all configurations of defects possible. The functioning plate shall have the ability to determine that all sensors are functioning. The functioning plate must be able to have the ability to represent both through holes and soil side corrosion. Since the plate is used only for instrument functioning, the functioning plate used for a coated tank bottom may be a bare plate or a nonferrous material may be placed on top of the plate to simulate coating.
This equipment makes use of very powerful rare earth magnets. When disassembling the unit or moving the magnetic carriage great care should be exercised to prevent damage to either the equipment or injury to the operator. All tools should be kept well away from the magnetic bridge until required. Maintenance work should always be carried out on a wooden work bench.
The achievable sensitivity of any Flux Leakage Inspection on any given floor is directly dependent on the overall top surface condition. In ideal conditions it is possible to find very small corrosion areas on the underside of the plate. As the top surface deteriorates in regard to cleanliness, topside corrosion
and/or floor plate curvature the achievable inspection will become relatively less sensitive and the
results more and more unreliable. Every effort must be made to ensure that the top surface is as clean as possible and free from any product residue, rust or loose scale. The effect of any undulations or buckling of the floor plates must be taken into account in the assessment of indications and in the scanning method.